Курсовая работа: Расчет и проектирование механизма поворота руля
3. Расчет конической
прямозубой передачи
Привод от
электродвигателя .
Мощность, подводимая к
валу шестерни .
Частота вращения шестерни
.
Срок службы .
Принимаем число зубьев шестерни
равное .
По заданному
передаточному отношению вычисляем число зубьев колеса:
.
Определяем частоты
вращения и угловые скорости валов:
— ведущего:

— ведомого:
.
3.1 Проектировочный
расчет
Определение числа циклов
перемены напряжений колеса и шестерни и числа зубьев эквивалентных
цилиндрических колес
Числа циклов перемены напряжений шестерни и колеса:


где и - количество
контактов зубьев шестерни и колеса соответственно за один оборот (принимаем их
равными 1).
Определим
числа зубьев эквивалентных цилиндрических колес:
;
.
Определение
допускаемых напряжений
Определение
контактных допускаемых напряжений
,
где - предел контактной
выносливости

- коэффициент безопасности при
объемной закалке равен 1,1.
- коэффициент, учитывающий
шероховатость поверхности сопряженных зубьев, принимают в зависимости от класса
шероховатости: для 8-го класса - .
- коэффициент долговечности, так
как и , то
Принимаем окружную
скорость ,
тогда для открытых передач для .

.
В качестве расчетного
значения принимаем .
Определение изгибных
допускаемых напряжений
,
так как и , то .
Коэффициент безопасности
при работе зубьев на изгиб
,
где - коэффициент,
учитывающий нестабильность свойств материала зубчатого колеса и степень
ответственности передачи;
(для поковок) - коэффициент,
учитывающий способ получения заготовки колеса.
Тогда
.
- коэффициент, учитывающий шероховатость
переходной поверхности зуба. Для шлифованных и фрезерованных зубьев при классе
шероховатости не ниже 4-го .
- коэффициент, учитывающий
упрочнение переходной поверхности зуба. При отсутствии упрочнения .
- коэффициент, учитывающий
влияние двухстороннего приложения нагрузки: - при работе зубьев одной
стороной
по 
.
Определение предельных
допускаемых напряжений

.
Определение коэффициентов
расчетной нагрузки
Коэффициенты расчетной
нагрузки соответственно при расчетах на контактную и изгибную выносливость
,
где и - коэффициенты
неравномерности распределения нагрузки по длине контактных линий ;
- коэффициенты динамичности
нагрузки .
Определение среднего
диаметра шестерни по начальному (делительному) конусу
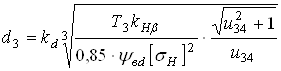
где по - коэффициент ширины
шестерни относительно ее диаметра;
- для стальных колес при
20-градусном зацеплении без смещения рекомендуется принимать при расчете
прямозубых конических передач.
Вращающий момент на валу
колеса:
.
Таким образом,
.
Из конструктивных
соображений принимаем .
Определение модуля в
среднем сечении зуба, конусного расстояния и внешнего окружного модуля
Модуль в среднем сечении
зуба
.
Конусное расстояние
,
где - ширина зубчатого
венца.
Внешний окружной модуль

Округляя это значение до
ближайшего стандартного по ГОСТ9563-60, получаем .
Уточняем и :
;

3.2 Проверочный расчет
Проверка передачи на
контактную выносливость
,
- коэффициент,
учитывающий форму сопряженных поверхностей зубьев;
- коэффициент,
учитывающий механические свойства материалов сопряженных колес;
- коэффициент,
учитывающий суммарную длину контактных линий.
Уточняем окружную
скорость:
.
Уточняем коэффициент
расчётной нагрузки:
,
- удельная окружная динамическая
сила;

- коэффициент, учитывающий
влияние вида зубчатой передачи и модификации профиля зубьев;
- коэффициент, учитывающий
влияние разности основных шагов зацепления зубьев шестерни и колеса;
- удельная расчётная
окружная сила в зоне наибольшей концентрации;
- полезная окружная сила.
Cследовательно,
;
;
.
Определю удельную
расчётную окружную силу:
,
,
таким образом, недогрузка
3,2%.
Проверка зубьев передачи
на изгибную выносливость

Определю коэффициенты
формы зубьев шестерни и колеса:
для 
для 
, ,
так как 84,7<90,6
проверяем зуб шестерни:
.
,
где - коэффициент,
учитывающий перекрытие зубьев, при 5-й степени точности
; ;
- коэффициент, учитывающий наклон
зубьев
.
Определение геометрических и других размеров колеса и шестерни
Половины углов при вершинах делительных (начальных) конусов шестерни и
колеса находим из равенства
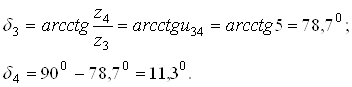
Конусное (дистанционное) расстояние .
Диаметры вершин зубьев по большому торцу равны:
;
.
Диаметры окружностей впадин по большому торцу равны:
;
.
Углы головок и ножек зубьев шестерни и колеса соответственно равны
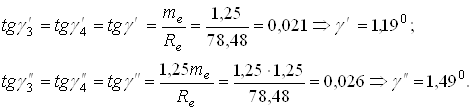
Половины углов конусов вершин зубьев (конусность заготовок) шестерни и
колеса соответственно равны:
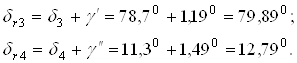
Определяем диаметр
отверстия под вал в колесе:
,
,
.
Принимаем из
конструктивных соображений .
4. Проектировочный и проверочный
расчет некоторых деталей и узлов
4.1 Тепловой расчет
Необходимо провести
проверку температуры масла в редукторе, которая не должна
превышать допускаемую . Температура воздуха вне корпуса
редуктора .
Температура масла в корпусе цилиндрической передачи
при непрерывной работе без искусственного охлаждения определяется по формуле:
,
где - площадь теплоотдающей
поверхности корпуса редуктора;
=9…17Вт/( )- коэффициент теплопередачи.
< .
4.2 Проверка по критерию
"теплостойкость"
Определение количества
тепла, образующегося вследствие потерь мощности.
,
где h=0,918% – КПД редуктора;
– мощность на ведущем вале:
.
Таким образом,
.
двигатель
передача редуктор шкив
4.3 Расчет валов
Основными условиями,
которым должна отвечать конструкция вала являются достаточная прочность,
обеспечивающая нормальную работу зацеплений и подшипников; технологичность
конструкции и экономию материала. В качестве материала для валов используют
углеродистые и легированные стали.
Расчет вала выполняется в
четыре этапа:
·
Ориентировочный
расчет на кручение;
·
Расчет на сложное
сопротивление (кручение, изгиб);
·
Расчет на
выносливость.
За материал валов
принимаем сталь 12ХН3А, с характеристикой:
- временное сопротивление разрыву;
- предел выносливости при
симметричном цикле напряжений изгиба;
- предел выносливости при симметричном
цикле напряжений кручения;
-коэффициенты чувствительности
материала к асимметрии цикла напряжений соответственно при изгибе и кручении.
Ориентировочный расчет
валов на кручение
Определим потребный
диаметр вала на ведущем шкиве учитывая прочностные характеристики.
где Т – крутящий момент на
валу
[tкр] – допускаемое напряжения при
кручении.
Так как расчётная
величина является очень малой конструктивно для удобства и возможности
шпоночного соединения выбираем вал с d=10 мм, при этом выигрывая большой запас
прочности и такой же диаметр имеет вал электрического двигателя, а это упрощает
задачу конструирования.
Определим потребный
диаметр вала на ведомом шкиве учитывая прочностные характеристики.
Принимаем диаметр вала d=15 мм, это нам даст большой запас
прочности и облегчит задачу проектирования.
Определим потребный
диаметр тихоходного вала конического редуктора учитывая прочностные
характеристики.
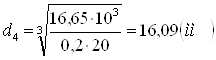
Принимаем диаметр вала d=20 мм, это нам даст большой запас
прочности и облегчит задачу проектирования.
Расчет валов на сложное сопротивление
Для расчета вала на
сложное сопротивление необходимо составить его расчетную схему:
- разметить точки, в
которых расположены условные опоры;
- определить величину и
направление действующих на вал сил: окружной , радиальной , осевой . А также точки их
приложения.
Приведем расчет
тихоходного вала (поз.13):
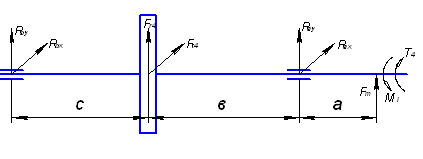
Рис.3 – Расчетная схема
тихоходного вала на сложное сопротивление
Длины расчетных участков
находятся после предварительного проектирования:

Реакции опор для входного
вала:


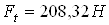
Определим реакции опор:
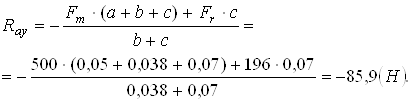
.
.
.
Построим эпюры моментов
для тихоходного вала:
Изгибающие моменты в
горизонтальной плоскости:
.

.
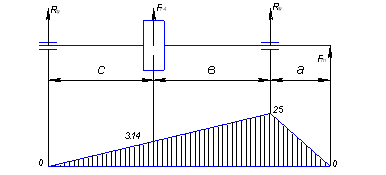
Рис.5 – Эпюра изгибающего момента в
горизонтальной плоскости для тихоходного вала
Максимальный изгибающий
момент действует в сечении III – .
Изгибающие моменты в
вертикальной плоскости
.
.
Максимальный изгибающий
момент действует в сечении II – .
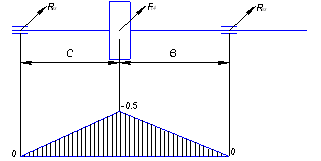
Рис.6 – Эпюра изгибающего
момента в вертикальной плоскости для тихоходного вала
Построим эпюру крутящего
момента для быстроходного вала.
.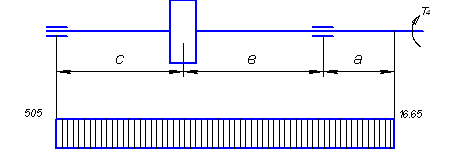
Рис.7 – Эпюра крутящего
момента для тихоходного вала
Приведенный момент

Максимальный приведенный
момент
;
.
Наиболее опасным является
третье сечение.
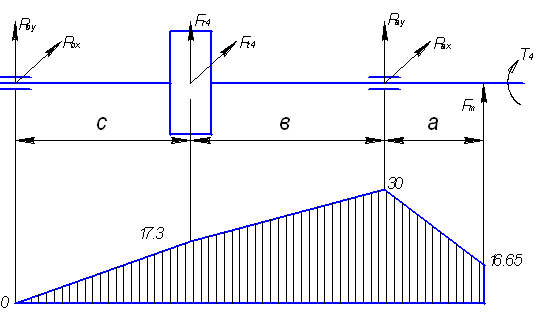
Рис.8 – Эпюра приведенного
момента для тихоходного вала
Расчет валов на
выносливость[1]
Для примера будем
рассчитывать тихоходный вал.
Определим коэффициент
запаса прочности быстроходного (рис.13) вала
двухступенчатого цилиндрического редуктора.
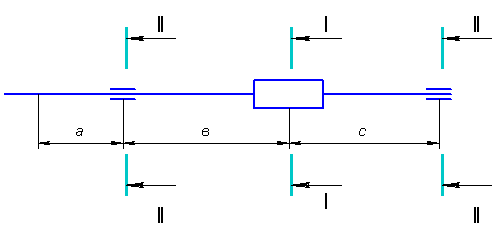
Рис.9 – Расчетная схема
тихоходного вала на выносливость
1.а) Проверяем запас
прочности по пределу выносливости в сечении I-I. Концентрация
напряжений в этом сечении обусловлена наличием шестерни. Находим эффективные
коэффициенты концентрации напряжений при изгибе и кручении от шестерни. При , ; масштабный
коэффициент для вала ; коэффициент состояния
поверхности при шероховатости . Эффективный коэффициент
концентрации напряжений для данного сечения вала при изгибе и кручении в случае
отсутствия технологического упрочнения:
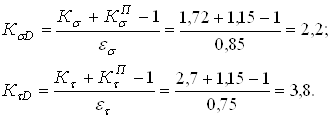
б) Находим запас
прочности для касательных напряжений.
Напряжение кручения
.
Амплитуда и среднее
значение номинальных напряжений кручения
.
Запас прочности для
касательных напряжений 
.
2. Определяем эффективные
коэффициенты концентрации напряжений при изгибе и кручении вала в сечении II-II, вызванные посадкой внутреннего кольца подшипника на вал.
Для вала с ,
.
Определяем запас
прочности для касательных напряжений:
,
здесь напряжение кручения:
,
амплитуда и среднее значение номинальных напряжений
кручения
.
4.4 Расчет подшипников
на долговечность
Основные критерии
работоспособности подшипников качения – его динамическая и статическая
грузоподъемности. Метод подбора по динамической грузоподъемности применяют в
случаях, когда частота вращения кольца превышает .
Исходя из конструкции
механизма, подбираем:
1) шариковый однорядный
подшипник (поз.18) номер 1000904 ГОСТ 8338-75:

Необходимо обеспечить
номинальную долговечность при условии, что 
а) Выбираем коэффициенты X и Y. Отношение этому соответствует [7, табл.
12.26] .
Поскольку ,
то .
б) Определяем
эквивалентную нагрузку
.
в) Определяем расчетную
долговечность по формуле:
,
где - показатель степени: - для
шарикоподшипников; - для роликоподшипников.
Такая расчетная
долговечность приемлема.
4.5 Расчет шпоночного
соединения
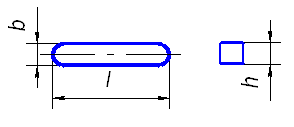
Рис.9 – Призматическая
шпонка
Принимаем на быстроходном
валу призматическую шпонку с размерами , длина шпонки по ГОСТ 23360-78 (поз.16).
Выбранную шпонку проверяем на смятие:
,
где - передаваемый момент;
- диаметр вала;
- допускаемое напряжение на
смятие: при стальной ступице и спокойной нагрузке ; при чугунной – вдвое меньше. В
случае неравномерной или ударной нагрузки на 25-40% ниже.
Проверим на смятие
призматические шпонки на тихоходном валу.
а) призматическая шпонка
с размерами ,
длина шпонки по ГОСТ 23360-78 (поз.43):
.
б) призматическая шпонка
с размерами ,
длина шпонки по ГОСТ 23360-78 (поз.39):
.
4.6 Проверочный расчет
болтов крепления двигателя к корпусу

Tкр = Tдв.
Мтр > Tдв.
Мтр = кÄTдв
Мтр =FзатÄfÄZÄD/2
К – коэффициент запаса;
Tдв – крутящий момент
двигателя;
f = 0.15…0.2 коэффициент
трения в стыке деталей
Z – количество болтов
соединения
Определим диаметр болтов
из условия прочности на срез:
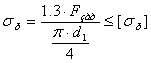
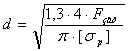
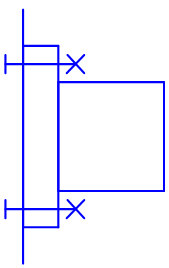
Материал болта: Ст. 3
sв = 380 МПа
sТ = 220 МПа
s-1 = 130 МПа
Определим допускаемое
напряжения
[sр]=0.3ÄsТ=0.3Ä220=66МПа
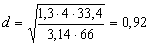
Выбираем болт М8
относительно габаритов двигателя.
5. Смазывание
подшипников и передач
Смазка подшипников
качения предназначена для уменьшения потерь мощности на трения, демпфирование
нагрузки, снижения риска износа и коррозии контактирующих поверхностях,
уменьшения шума и лучшего отвода теплоты, заполнения зазоров в уплотнениях,
обеспечивая этим герметичность подшипникового узла. Применяют жидкие
(минеральные масла и др.) и пластичные (солидолы, консталины и др.) смазочные
материалы.
На практике стремятся
смазывать подшипники тем маслом, которым смазывают детали передач. При
внутренней смазки колёс подшипники качения смазывают брызгами масла. При
окружной скорости колёс u= 1 м/с брызгами масла покрывают все детали передачи и внутренние
поверхности стенок корпуса. Стекающее с колес, с валов и со стенок корпуса
масло попадает в подшипники.
Минимальный уровень
масляной ванной ограничивают центром нижнего тела качения подшипников. В ряде
случаев для обеспечения надежного смазывания зацепления шестерню или червяк и
подшипник быстроходного вала погружают в масло. В этом случае избегание
попадания продуктов износа передачи зубчатых колес, червяков и др., а также
излишнего пожива маслом подшипники защищаются маслозащитными кольцами и
мембраной. Особенно если на быстроходном валу установлены косозубые или
шевронные колёса либо червяк, т.е. когда зубья колес или витки червяка гонят
масло на подшипник и заливают его, вызывая разогрев последнего.
Добавления жидкого масла
производят не реже одного раза в месяц, а через каждые 3…6 месяцев полностью заменяют.
Пластичные смазные
материалы применяют при окружной скорости колёс u= 1 м/с для смазывания опор машин,
работающих в среде, содержащей вредные смеси и примеси, и там, где необходима
работа машин (в химической, пищевой и текстильной промышленности).
Учитывая все
вышесказанное для нашего механизма мы выбираем такую смазку как ”Солидол С”.
ГОСТ 4366-64
Предельная прочность на
сдвиг, г/см2.
20Å - 2-6
50 - 2-4
Вязкость при tÅ
0Å <= 2000
20Å <=400-1000
водостойкость - хорошая
tÅ применяемая -30Å - 70Å
6. Компоновка и
разработка чертежа редуктора
Размеры валов и
подшипников в значительной мере определяются компоновочными размерами
прямозубых цилиндрических и конических передач, взаимным расположением
агрегатов привода, заданными габаритными размерами привода.
Поэтому после расчета
передач и установленных размеров их основных деталей приступают к составлению
компоновочных чертежей узлов, агрегатов и всего привода.
Компоновка привода
определяется его назначением, предъявленными к нему требованиями, зависит от
компоновки отдельных агрегатов.
Механизм в данном проект
можно оставлять стандартным (протоколом М2), но учитывая особенности расчётов.
Конструкция механизма поворота руля робота показана на формате А1 в приложении
к курсовой работе.
Конструкция выполняется
по расчетам, но выбирается по конструктивным соображениям и стандартами с явным
запасом прочности. Это облегчает задачу проектирования механизма, но этот
проект даёт только навыки к проектированию. На самом деле при более серьезной
проектировке надо рассчитывать каждый элемент механизма и, по возможности,
выбирать таковой согласно стандартом.
Заключение
При
выполнении данного курсового проекта мы приобрели навыки в проектировании и
конструировании механизмов и деталей машин, а также навыки в использовании
справочной литературой.
Рассчитывались коническая
и зубчатая ременная передачи. Все параметры были рассчитаны и подобраны в
соответствии с ГОСТами, что несомненно облегчит сборку данного модуля на
производстве и обеспечит качественную его работу.
Такая схема модуля
поворота руля применяется часто. Зубчатая ременная передача в совокупности с
конической передачей позволяет обеспечить высокую точность позиционирования,
тихоходность и сравнительно небольшие потери мощности.
При более глубоком подходе
к проектированию механизма нужно пересмотреть корпусные детали, направляющие и
соединительные элементы и детали.
Список используемой
литературы
1. Киркач
Н.Ф., Баласанян Р.А. Расчет и проектирование деталей машин, Х.: Основа, 1991,
276с.
2. Анурьев В.И. «Справочник
конструктора-машиностроителя» (3 тома). М.,1980.
3.Назин В.И. Проектирование механизмов роботов.- Х: «ХАИ»,
1999 – 136с.
4.Бейзедьман Р. Д., Цыпкин Б. В., Перель Л. Я. ”Подшипники
качения” (справочник),М. “Машиностроение”,1975, 574с.
5. Иванов М.Н. Детали машин. Учебн.М.: Высшая школа, 1984,
336с.
6. Чернин И.М., Кузьмин А.В., Ицкович Г.М. «Расчеты деталей машин» (справочное
пособие). Издание 2-е, переработанное и дополненное. – Минск: «Высшая школа»,
1978 – 472с.
7. Чернавский С.А., Снесарев Г.А., Боков К.Н. «Проектирование
механических передач». Учебно-справочное пособие по курсовому проектированию
механических передач. Издание пятое, переработанное и дополненное. – Москва:
«Машиностроение», 1984 – 560с.
|